Design For Recycling
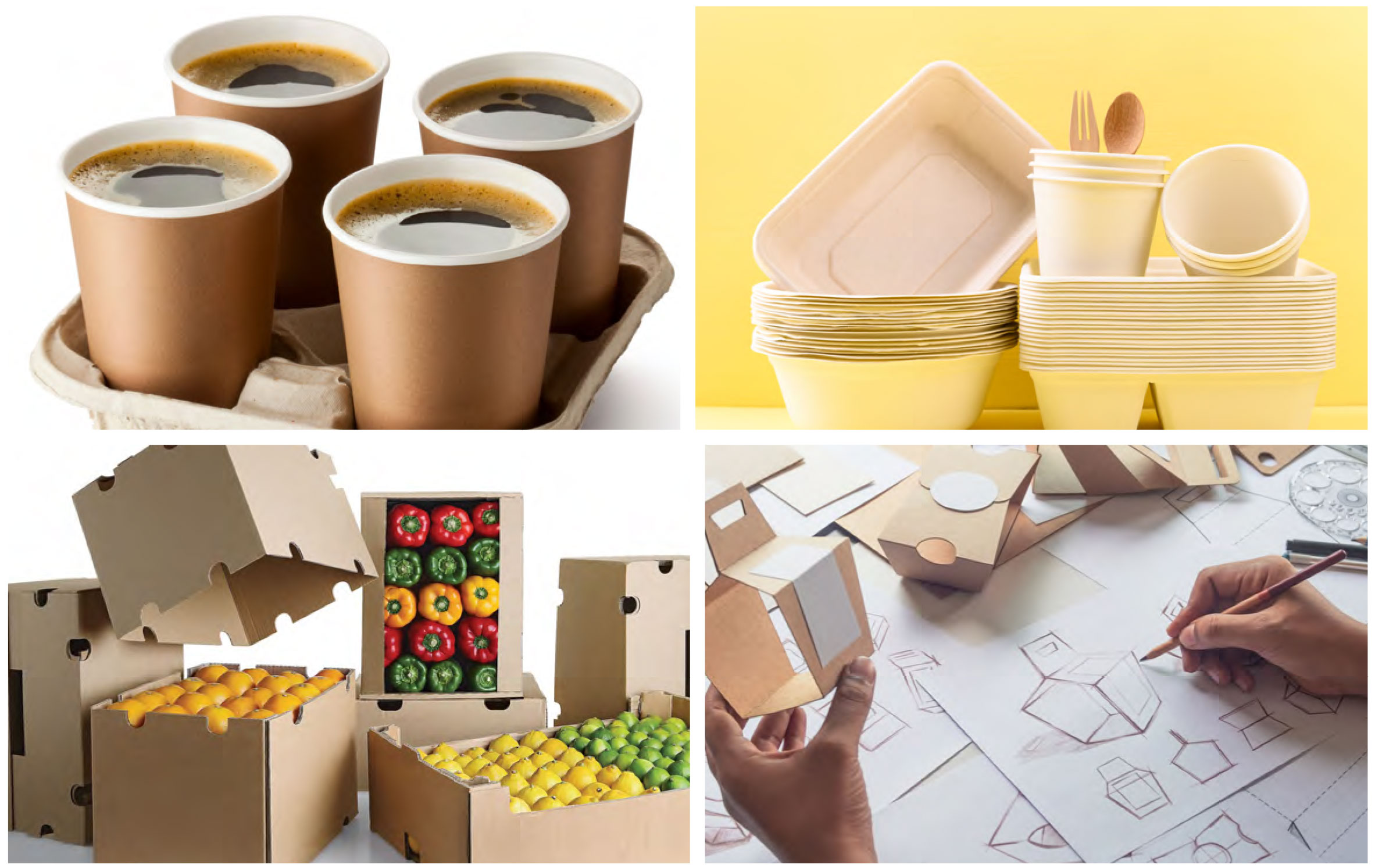
1.1. General introduction
Paper is essentially divided into two distinct categories: paper and paperboard. Paper is usually lighter in basis weight or grammage, thinner, and more flexible than paperboard. Its primary uses are for printing, writing, wrapping, and hygiene purposes, although this is just a short list. Paperboard – as the suffix hints – is heavier, thicker and more rigid.
Without paper and board, many of us would not be able to read, teach or learn; convey messages or market our products. We would not be able to ship merchandise, or protect goods, nor improve our lives with personal hygiene products and tissue. Across the world, wood, paper and tissue products touch lives every day and in ways we rarely notice.
Paper was first produced in South Africa in 1920 using imported recycled paper. In 1936, the straw was first used. Today, paper products are made from renewable virgin wood fibre or recycled paper fibre, and in cases using bagasse (sugar cane process waste).
In South Africa, the wood fibre for papermaking comes from sustainably managed commercial timber plantations. Species such as eucalyptus or pine are planted, harvested and replanted – much like farming. Less than 10% of the total plantation area is harvested each year, and replaced with new saplings or regrown (coppiced) in the same year. This means that there are compartments maturing each year, with a sustainable supply of wood for generations to come.
This makes wood (and paper) a renewable resource which stores carbon. Paper is also recyclable, which not only keeps the carbon stored for longer, but also provides paper manufacturers with an alternative source of fibre.
Today, wood fibre arrives at the mill as whole tree trunks, wood chips or paper pulp from other mills. Recycled or waste paper can also be used.
On average, South Africa collects 1.2 million tonnes of recoverable paper* and packaging, each year. (*Recoverable paper excludes paper which is unrecoverable or unsuitable for recycling. For example, toilet tissue and sanitary products, cigarette paper and archive material.)
Find latest paper recycling statistics here
1.2. The Process
The types of raw materials used, and the process employed to make the paper will produce different kinds of paper, depending on what the paper or paper board will be used for.
Each grade of paper has a weight, a processing type and a finish. These factors determine its transparency, appearance, weight, thickness, level of opaqueness, feel and durability. For example, the lifecycle of a newspaper is short. It’s not going to sit on your bookshelf for years, whereas a coffee table will be referred to often and requires a better finish.
The type of printing technology will also determine the type of paper that should be used.
1.2.1. Fibre
Paper can be made from any fibrous material prepared such as wood, cotton, grasses, etc. Today however it is largely produced using wood. In South Africa, this wood comes from eucalyptus (hardwood) and pine (softwood) trees.
1.2.2. Pulping
At the pulp mill, the logs are debarked and are ground to release fibres for mechanical wood pulp or wood chips are processed for chemical pulp. The objective of pulping is to break down and dissolve the lignin, the natural ‘glue’ that holds the wood together.
1.2.2.1. Chemical pulping
Wood chips are “cooked” in a digester at high pressure with an appropriate solution of chemicals to dissolve the lignin and separate the cellulose fibre bundles into individual cellulose fibres. Since chemical processing is gentle on the fibre, chemical pulps tend to have longer fibres and make strong paper such as printing and writing papers and paperboard. (Lignin is what makes paper turn yellow after a while.)
Paper made from chemical pulp and coated to ensure a smooth surface for printing is called coated fine paper (or wood free paper) and used in the production of calendars, coffee table books, magazines and business reports.
1.2.2.2. Mechanical pulping
Chemicals are not used to remove lignin. Instead, wood chips are pressed against a refiner that mechanically separates the fibres. Mechanical pulps have shorter fibre lengths and produce papers which do not require as much strength.
Paper made with mechanical pulp is used for newsprint, speciality papers, tissue, paperboard and wallboard.
1.2.2.3. Thermomechanical pulping
This is similar to mechanical pulping but takes place under higher temperature and pressure. This softens the lignin even more than can be accomplished using frictional heat, and fibre separation is easier.
1.2.3. Finishing
Coated vs uncoated paper – What’s the difference?
Coated papers contain a layer of coating material on one or both sides. This “seals” the paper, restricting ink absorption by the paper. The ink can sit on top of the paper, in a crisp defined dot. The coating materials of pigments and fillers help to improve the printing surface of the paper.
Uncoated papers – not coated with a layer of pigment – usually include printing and writing papers made from bleached chemical pulp. They are used for general printing, photocopying and stationery. As they are more porous, the ink will soak into the paper creating a softer, warmer appearance. Uncoated papers can be categorized by type: offset, opaque and text & cover.
1.2.4. Paper recycling
Paper recycling involves the reprocessing of paper products into new products. The feed stocks would either be post-production/pre-consumer sources (offcuts or rejects from the papermaking, conversion or printing phases) or post-consumer sources, i.e. after a consumer has used it.
Generally, recovered paper is used to make different grades of paper. Recyclable paper and board is separated into 16 different categories which are listed in the Appendix at the back of this section. Paper would be sorted and baled according to grade and processed depending on the type of “new paper” being made.
The recovered paper is fed onto conveyors where obvious contaminants (e.g. metals, rubber etc.) are removed. The paper is then fed into a pulper – a giant industrial blender – to process recycled paper into a pulp slurry. The pulp is then passed through a variety of screens to extract other contaminants before being delivered to the paper machine.
Paper fibre tends to shorten each time it is repulped and refined. Once paper fibres become too short, they will pass through the sieves and be classed as sludge. It is for this reason that virgin fibre will be added to “boost” pulp recipes and add strength.
According to Kreplin, Schabel and Putz (December 2019), fibres from corrugated boxes can be recycled 25 times without experiencing signs of a “recycling collapse”. Depending on the specific fibre-based product/fibre type and the corresponding recycling processes and losses during recycling, the average number of cycles can be lower. Introducing virgin fibres helps to maintain pulp volume, quality and mechanical properties. (Source: Circularity by Design for Fibre-Based Packaging, 4evergreen)
All manufactured paper is 100% recyclable, such as:
- office paper
- magazines, including glossy magazines
- brochures
- newspapers
- corrugated cardboard
- cardboard boxes such as cereal boxes
- shredded paper (not always recommended as it is difficult to bale and it shortens the paper fibres)
Some paper products are recycled but they may be difficult to recycle or there is limited capacity or technology to do:
- liquid packaging board – milk and juice cartons
- paper cups and containers
- frozen food containers – particularly those with PE coatings
- label release liners and backing papers
- potato sacks and cement bags
Paper becomes non-recyclable when:
- additives for wet strength are used in the paper manufacturing process.
- heavy foils and embellishments are added (i.e. gift wrap; cards, luxury packaging).
- glues are added e.g. some sacks with glued inner sleeves and ‘sticky’ notes.
- wax coating, foil linings or laminates are added to boxes.
- plastic (PE) protective layers are added e.g. tile cement bags, dog food bags.
- when used in a manner that food or automotive oils impregnate (contaminate) the paper.
- when flushed down the toilet, as tissue paper.
Contaminants – or more importantly “non-recyclable materials” – such as those indicated above can affect the reprocessing of the paper. It is for this reason that paper should ideally be kept free from such materials. Considerable research is being done in SA to try to deal with some of these materials. Ideally all players within the paper chain including packaging converters and printers should be mindful of the current constraints.
1.3. Paper grade definitions for recycling
This list of South African Standard Grades of Recovered Paper and Board gives a general description of the standard grades by defining what they do and do not contain.
Refer to the Paper Grade Definitions here.
1.3.1. Moisture content in recovered paper and board
Recovered paper and board will in principle be supplied with moisture of not more than the naturally occurring level – where the moisture content is higher than 10% on paper and 12% on kraft/board (of air dried weight), the additional weight in excess of the allowed percentage may be claimed back.
A guideline document for paper-based packaging and product design in South Africa
1.4. Used for Recovered Paper
RECOVERED
- Corrugated boxes
- Newspapers and magazines
- Office paper, newspaper, magazines, printer off-cuts
- Office paper, corrugated boxes, newspaper, carton board trims, printer off-cuts
- Newspaper, carton board trims
- Liquid board packaging
- Milk and juice cartons – 75% virgin paper board + 25% polyethylene and aluminium (poly/al)
- Paper cups – 95% virgin paper board + 5% polyethylene (PE) coating
RECYCLED INTO
- New corrugated boxes
- Newspaper
- Bath tissue products. Kitchen and industrial paper towelling
- Carton board – cereal boxes, soap carton
- Moulded paper products i.e. egg boxes
- Paper board used in new paper packaging
- Poly/al and PE – various plastic injection moulded products
Table 8: Different types of uses for paper
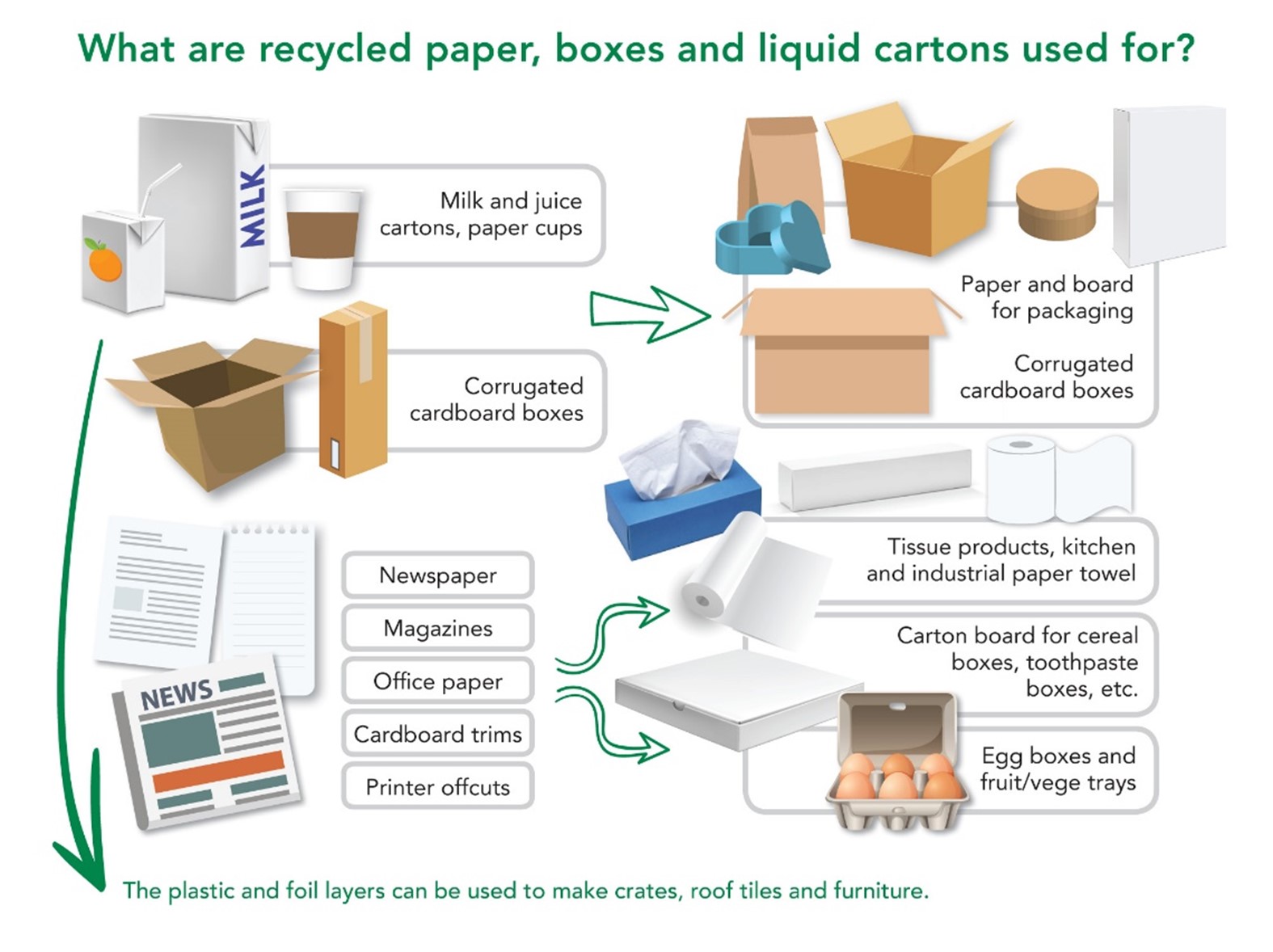
Figure 2: Uses of recycled paper, boxes and liquid cartons
1.5. Elements Added To Paper Or Paper Packaging To Enhance Functionality
1.5.1. Ink coverage
For white paper which is largely used for tissue products or blended into fine paper production, the mills have de-inking plants which can deal with a normal amount of ink coverage. As with other contaminants, excessive ink coverage can cause bottlenecks or interruptions in production. Heavily inked papers will be recycled but as a lower grade paper.
1.5.2. Adhesives
The system deals with water-based adhesives without difficulty, but latex or hotmelt adhesives can stick to the cylinders on the paper machines, causing holes in the paper produced. Such contaminants are known as ‘stickies’. This is more serious for lightweight papers and tissue. Some of the paper mills have upgraded their equipment to deal with the adhesives (hotmelt glues) found in spines of magazines but these could be a problem for smaller paper producers.
1.5.3. Wet-strength additives
Certain papers (e.g. potato sacks) contain additives to prevent the paper breaking up in moist conditions. These are recyclable in a liquid packaging recycling plant however they are not commonly recycled. An inhibiting factor for recycling is identification and sorting. Ideally packaging should clearly state that it contains wet strength additives.
1.5.4. Liquid board packaging– beverage cartons
Milk, juice and certain food cartons are made up of a combination of paper board, polyethylene and aluminium (PolyAlu) or paper board and a polyethylene (PE) plastic lining.
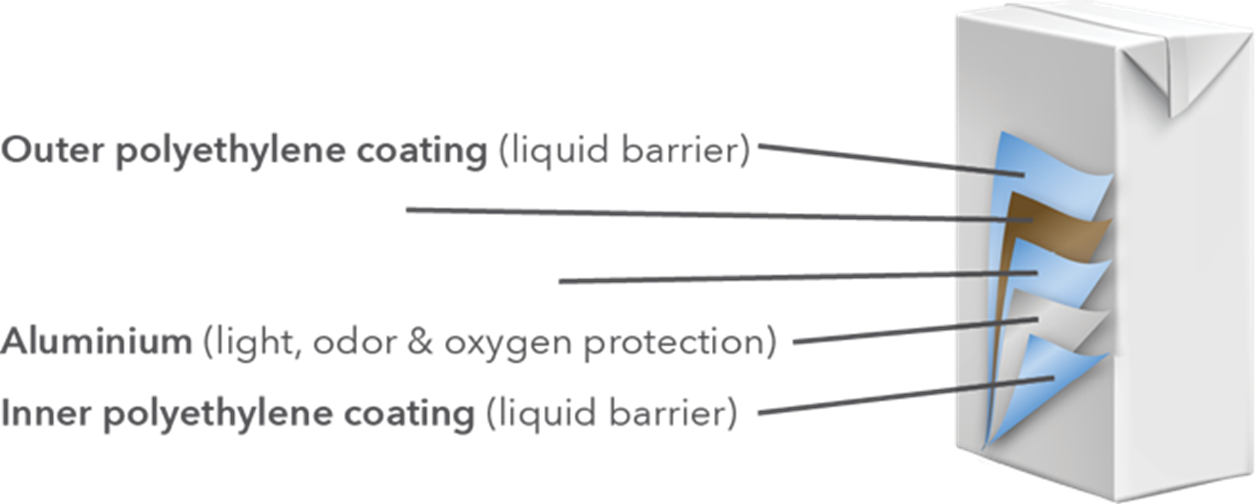
Aseptic/shelf-stable cartons
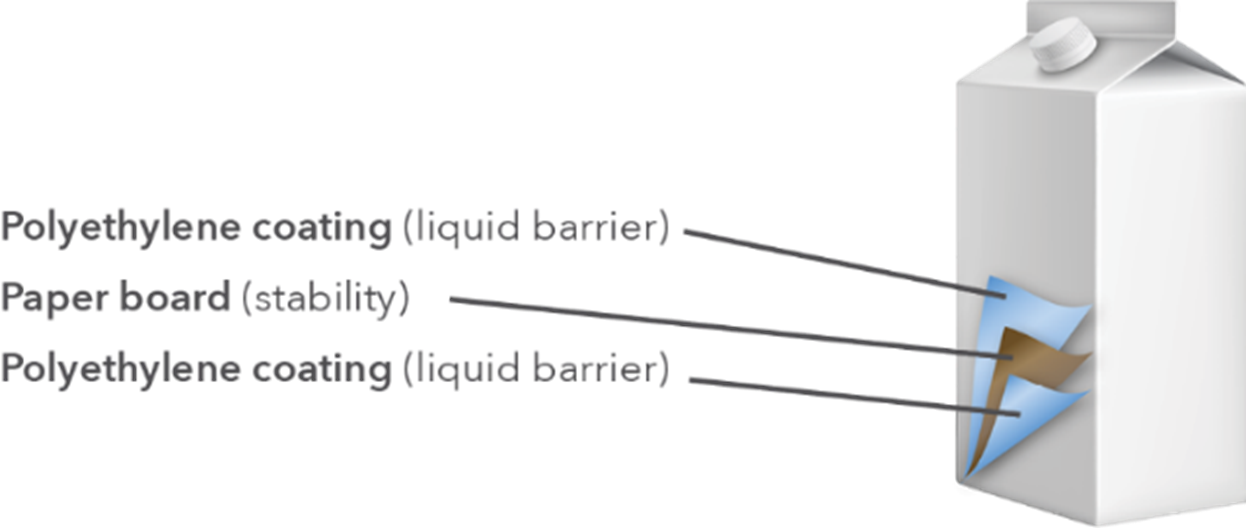
Refrigerated/gable-top cartons
Figure 3: Composition of a beverage carton
Paper board is the dominant component and is made from imported virgin board making it attractive recoverable paper fibre.
Bales of recovered liquid board packaging are fed into a specially designed hydropulper that rubs the paper fibre away from the PolyAlu or PE layers. The fibre is then used to manufacture recycled paper board for various end uses. The PolyAlu and plastic, including the closures and straws, is processed further into various plastic injection moulded products. Lids of milk cartons, for instance, can be used to make wheelie bins.
1.5.5. Liquid board packaging – paper cups
Paper cups are also a form of liquid packaging. Cups are made mostly from paperboard. A thin layer of polyethylene (PE) lines the inside, making them liquid proof and providing function.
Hot cups
- Usually two layers of paperboard for insulation.
- One layer of PE lining on the inside.
- Some hot cups are single walled but usually come with a sleeve.
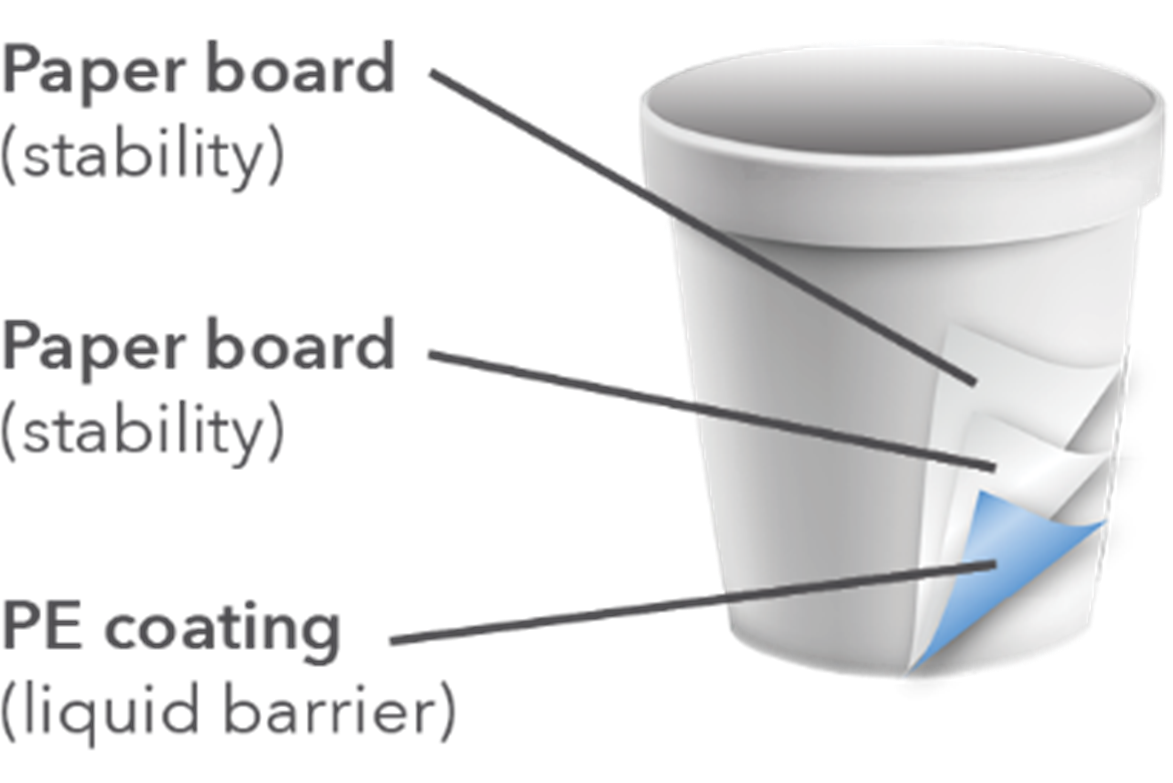
Figure 4: Hot paper cup composition
Cold cups
- One layer of paperboard.
- Outer layer of PE to handle condensation while an inner PE layer prevents leaking.
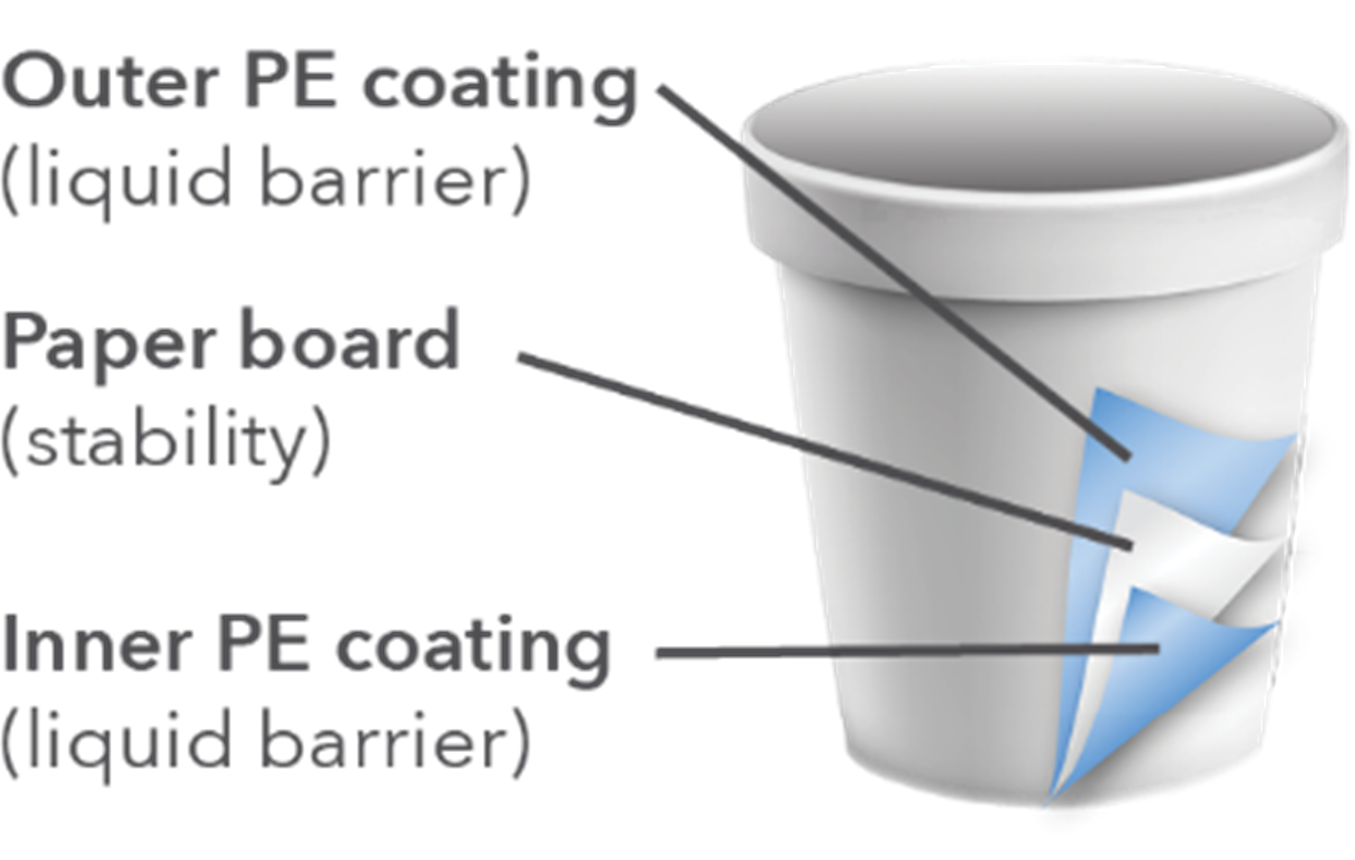
Figure 5: Cold paper cup composition
Paper cups and biodegradability
Some paper cups may be labelled as biodegradable or compostable. This means that the paperboard is coated with a starch-based lining called polylactic acid (PLA) instead of a plastic lining.
Compostability or biodegradability refers to environments with specific conditions such as those found in industrial composting facilities (airflow, temperature and moisture) and it is unlikely that these conditions will occur naturally. While this lining will biodegrade over time, unless in these specific environments, this might be a much longer period than anticipated. Generally, EU standard EN13432 is used as reference.
As this product is designed to decompose and break down, generally speaking, biodegradable or compostable plastic is not suitable for recycling as it “contaminates” the plastic recycling stream – if an end product is made with non-biodegradable plastic and biodegradable plastic, this could reduce the integrity of the product, with parts of it breaking down.
Biodegradable VS Compostable
All compostable products are biodegradable, but not all biodegradable products are compostable.
Compostable products are made by organic elements or plants that can degrade with time. For example, cellulose, corn starch, bagasse, and others. Compostable products produce humus upon degradation, which is the richest and most important part of all soils. The high level of microbial activity in humus boosts beneficial microbes within the soil which, in turn, assists plants to strengthen their immune systems (Nature’s Path, 2020). Therefore, compostable products do not release any toxic element to the environment after degradation.
Biodegradable is a term mainly used in the plastics industry, where the material breaks down into microplastics faster than regular plastic, under any conditions (compost, landfill, soil). It is possible to find biodegradable products made from plant-based materials (like corn oil, or starch) or petroleum-based plastic which are easier to degrade. Compared with the composting process, biodegradable products can take several months to break down and some recent studies found that some of these products degrade to leave harmful substances behind such as microplastics. Even if you cannot see it, these micro materials have components toxic to our environment. (Source: Ocean Watch)
Compostable products have undergone strict testing to ensure that they break down within a specific time frame and under certain conditions such as the right degree of temperature, moisture and air flow. Such products do not release anything harmful into the environment. Biodegradable products have no such requirements, meaning that they may not be as beneficial as they first appear. (Source: Elevate Packaging)
Useful resources
- Biodegradable and Compostable Packaging: A review of the South African landscape (Moss Group on behalf of The South African Initiative to End Plastic Waste)
- Design and Management for Circularity – the Case of Paper (World Economic Forum)
1.5.6. Laminates and wax layers
Liners are applied separately from the board production. Recycling companies don’t particularly want a wax material as this would melt back into solution during the pulping process and would be very difficult to remove. The wax would form into stickies and cause runnability problems on the paper and board machines.
Extensive research is carried out by the various centres to improve both the environmental sustainability and the performance of the packaging.
1.6. Recycling Compatibility Matrix With Examples
The table below details the various grades in terms of their recyclability.
Green indicates that they are compatible with local recycling technology and thus can be recycled easily. The yellow indicates that they can be recycled locally but require some sort of pre-treatment or special interventions to process the product and extract the fibres. The orange indicates that the products are considered difficult to recycle using available technology, or that there is limited capacity or availability of the required technology.
Fully compatible with standard recycling process
Packaging papers
- Corrugated containers and cardboard boxes
- Kraft paper
- Fluting – middle liner in a sandwich of liner board or supplied separately as protective packaging.
- Whitetop liner – white outer surfaces for printing and grey or brown inner surface
- Folding boxboard – board that is folded into various sizes and shapes of packaging for health and beauty products, foods, confectionaries, pharmaceuticals, graphic uses and cigarette packaging.
- Recyclable paper sacks and bags (grocery and take-away bags without wet strength additives)
Printing and writing grades
- Office paper
- Newsprint, magazines
- Coated/graphic papers
Conditionally compatible with standard recycling process
Items added to packaging to enhance functionality for the product that it will contain. The additions can influence the efficiency of the recycling process or compromise the quality of the fibre output.
Paper products that comprise:
- Temporary wet strength agents
- Siliconising agents
- Barrier coatings
- Adhesives
- Security labels, etc
Necessitates a specialised mill or pulping technology or requires more R&D and investment
These products have elements that are difficult to separate from the paper fibre using standard recycling process.
- Used beverage cartons (liquid board packaging)
- Paper cups and containers
- Frozen food packaging
- Wet strength paper sacks (cement and potato bags)
- Plastic-based label backing papers
Glassine label backing paper and waste matrix
Table 9: compatibility with standard recycling process
1.7. Designing for recyclability
When designing a paper-based product or packaging, it is important to understand the degrees to which certain attributes should be used.:
Printing and Writing Paper
GREEN | ORANGE | RED | |
Safe to use in terms of compatibility with recycling process, as per above table (indicated as green) | Should be used with care, or limited | As far as possible, avoid using or applying to paper-based products and packaging | |
Tinted Paper | Pastel Colour | Heavily dyed | |
Inserts in Magazines | Same paper used through the product | Different paper types in a single product | |
Inks | Excessive coverage | Heavy Metal Metallic | |
Adhesives | Water Based | Latex/Hotmelt Self-Adhesive |
|
Laminates on Envelopes | Window carbonless papers Non-cellulose/non-paper envelopes |
Wax Label backing papers (release liner) |
Corrugated Boxes Or Folding Box Board
GREEN | ORANGE | RED | |
Safe to use in terms of compatibility with recycling process, as per above table (indicated as green) | Should be used with care, or limited | As far as possible, avoid using or applying to paper-based products and packaging | |
Tinted Paper | Pastel Colour | Heavily dyed | |
Inserts in Magazines | Same paper used through the product | Different paper types in a single product | |
Inks | Excessive coverage | Heavy Metal Metallic | |
Adhesives | Water Based | Latex/Hotmelt Self-Adhesive |
|
Laminates on Envelopes | Window carbonless papers Non-cellulose/non-paper envelopes |
Wax Label backing papers (release liner) |
Other Packaging
Adhesives | Water Based | Latex/Hotmelt Adhesive labels Liquid board Packaging cartons (with plastic and aluminium layers) Wet strength paper Polycoat Wax Foil lined papers coated Windows |
|
Laminates/ additives |
Sacks containing free film | ||
Features Office paper ream Wrap |
Polycoat |